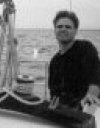
randallmayes
Submitted by randallmayes on
Due to emerging technologies, most sectors of the economy are expected to undergo a transformation over the next several decades, and manufacturing is no exception. As a result, manufacturing executives will have to make costly and crucial decisions on how to invest in the manufacturing revolution for their own manufacturing facilities. This could be is great news for manufacturing executives’ bottom line depending on how they forecast the path to the new manufacturing paradigm and invest accordingly.
It’s certain that 3D printing or additive manufacturing will supplement traditional manufacturing, but to what extent other emerging technologies will play is unsettled. As a result, so-called “smart factories” utilizing 3D printing could follow several major scenarios. These factories are smart because they provide the best technological solutions to existing problems, and that provides a clue to how they might evolve.
The Maker Movement
The third digital revolution—digital fabrication—builds on the previous two—communications and computation. Using CAD-CAM design plans and 3D printers enables individuals and small independent fab labs to print customized products relatively inexpensively by eliminating the middleman and reducing shipping costs, waste, and energy consumption.
In my hometown of Durham, NC, the maker movement is alive and well. At Duke University, maker labs are strategically placed all over campus to particularly entice humanities and social science students to roll up their sleeves and make physical products. Due to a cadaver shortage, the main maker lab houses a half million dollar 3D printer that produces anatomical parts with three different materials that medical students use for training.
Of the two shopping malls in Durham, one was reduced to rubble and the other has a noticeable amount of vacancies. Seizing on an opportunity, the university has leased the flagship store spaces for administrative offices, and the city library system has leased several spaces to sell used books and hold maker classes. Thanks to these classes, I have made my own keychain, and built a drone and a model car that runs on a fuel cell.
This trend has gained momentum at the international level. Sherry Lassiter, who runs the Fab Foundation at MIT, observed that since 2003 the number of fab labs is doubling every year and a half which follows Moore’s Law (Gershenfeld, Gershenfeld, and Cutcher-Gershenfeld 2017). The next big step within the movement is self-assembly based on biological processes which are necessary for colonization on Mars, according to Neil Gershenfeld of MIT.
Smart Manufacturing
Building on past industrial revolutions, some technology experts believe we are about to enter the Fourth Industrial Revolution. Coined by Klaus Schwab of the World Economic Forum, it is the emergence and convergence of synthetic biology, AI, and smart manufacturing.
Smart manufacturing utilizes 3D printing, 4D printing, 3D scanning, CAD-CAM software, and novel nanomaterials. 3D printing is cost effective for printing customized parts and products, and 4D printing uses sensors to modify the products specifications in response to environmental conditions. For parts without CAD-CAM design instructions, through 3D scanning it is possible to create them.
With sensors embedded in products and equipment and using accumulated data, data analytics can look for patterns in the data that match known failures and provide or schedule preventative maintenance to avoid down time in equipment. These manufacturing systems utilize the IoT, machine-machine interfaces, cloud storage, and emerging 5G networks to handle the large amounts of accumulated data and to process it rapidly. In the future, human-machine interfaces such as augmented and virtual reality could assist designers with prototyping and technicians with maintenance.
In 2012, Germany began its own smart manufacturing initiative referred to as Industry 4.0, and the German automotive industry was an early adopter. Industry 4.0 utilizes cyberphysical systems to create physical objects from digital technologies building on the previous three industrial revolutions—mechanization, mass production, and automation.
Pan-Industrials
With the current manufacturing platform, conglomerates and large corporations rely on economies of scale to produce standardized parts and offshore production using expensive production equipment and extensive supply chains.
In The Pan-Industrial Revolution: How New Manufacturing Titans Will Transform the World, Richard D’Aveni, a business strategy expert at Dartmouth’s Tuck School of Business, argues that new platforms built around additive manufacturing, which he calls pan-industrials with new ways to create value, will eventually dominate the global economy. Pan-industrials with new additive manufacturing platforms will literally turn the current manufacturing paradigm upside down since they will rely on economies of scope and local production using relatively inexpensive equipment, and reduce the supply chain.
Traditional manufacturing systems cost in the million dollar range and produce standardized parts. With high fixed costs and low variable costs, the advantage of economies of scale is the lower costs from mass production. Independent 3D printing shops will only be able to produce items in small quantities and will not be able to compete with pan industrials that can mass produce goods faster and more efficiently, according to D’Aveni.
Additive manufacturing has lower fixed costs with industrial 3D printers priced in the several hundred thousand dollar range and have higher variable costs. Since additive manufacturing lacks economies of scale and 99 percent of all manufactured parts are standardized, Oxford University professor Matthew Holweg points out that 3D printing will not be profitable for mass production or revolutionize the manufacturing sector (D’Aveni 2018).
While economies of scale add value through lower costs from mass production, economies of scope builds value through flexibility. Using downloaded design files, 3D printers can produce a diverse range of products for numerous industries. Currently, post production costs are up to 70 percent of the total cost of commercial 3D printing (D’Aveni 2018). To add further value, Germany manufacturers are building NextGenAM production facilities utilizing banks of specialized automated robotic arms which reduce time and costs in post-production.
Pan-industrials have moved beyond the concept stage and are in various early and mainstream stages of adoption with products ranging from plane and automobile parts to athletic shoes.
Who’s Leading the Manufacturing Revolution?
While companies will lead, survive, or perish based on their infrastructural investments, nations are also vying for leadership in manufacturing. In 2010, China surpassed the United States as the largest manufacturing country. However, interestingly neither China nor the United States are leading the way in advanced manufacturing.
Currently, the top three countries are Germany, South Korea, and Japan, and all have positive trade balances, according to a report by the U.S. National Science and Technology Council (Executive Office of the President 2012). Part of Germany’s success is due to President Angela Merkel's full support for Industry 4.0 applications by investing US$50 billion annually from 2015 through 2020.
The United States is fourth, followed by the United Kingdom, Canada, and Australia (Executive Office of the President 2012). According to a case study, innovation hubs in the United States are in a position to become more competitive at the international level. For example, Massachusetts has a history of innovation in manufacturing products and processes that enable it to transition into new market conditions. It has roughly 7,000 manufacturing firms with a highly skilled workforce near universities and research institutions, and 92 percent of its start-ups have fewer than 100 employees which have an entrepreneurial culture (Jeschke et. al. 2017).
References
D’Aveni, Richard. 2018. The Pan-industrial Revolution: How New Manufacturing Titans Will Transform the World. Houghton Mifflin Harcourt.
Executive Office of the President. A National Strategic Plan for Advanced Manufacturing. National Science and Technology Council. February 2012.
Gershenfeld, Neil, Alan Gershenfeld, and Joel Cutcher-Gershenfeld. 2017. Designing Reality. Basic Books.
Jeschke, Sabina, Christian Brecher, Houbing Song, and Danda B. Rawat (Editors). 2017. Industrial Internet of Things: Cybermanufacturing Systems. Springer.
Schwab, Klaus. 2016. The Fourth Industrial Revolution. World Economic Forum/Crown.